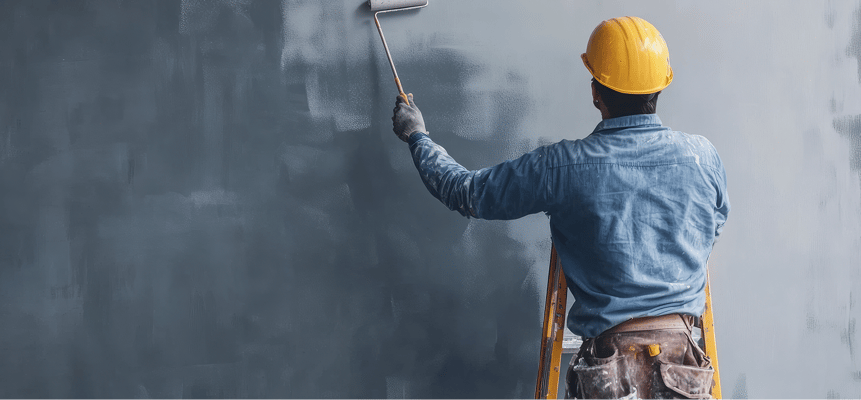
Blog
- All
- Preventative Maintenance
- Education
- Retirement Living & Aged Care
- Higgins News
- Strata & Body Corporate
- Contractor Management
- Paint Colours
- Planning & Project Management
- Sustainability
- Health & Safety
- Commercial Property
- Painting Costs & Quotes
- Commercial Buildings
- Healthcare
- Hotels & Resorts
- Antimicrobial Sanitising
- Community
- External Repaint
- Australian Capital Territory
- Brisbane
- Canberra
- Heritage Buildings
- High Rise Painting
- Sports & Recreation
23 Jun 2025 at 11:15 PM
Your guide to budgeting for commercial building painting
How much does it cost to paint a commercial building? It depends! Painting involves several cost factors that can vary...
Read More
02 Mar 2025 at 10:00 PM
How to manage apartment complex exterior painting projects
Apartment complex exterior painting might not seem like the most glamorous project on a Strata Manager’s to-do list,...
Read More
02 Feb 2025 at 10:00 PM
7 key considerations for choosing the right strata painters
Strata living is becoming increasingly common in Australia. According to the recent Australasian Strata Insights...
Read More
08 Jan 2025 at 10:00 PM
How to find good tradespeople you can always rely on
Running a busy facility means juggling endless maintenance tasks, but with limited time and budget, staying on top of...
Read More
01 Dec 2024 at 10:00 PM
Expert tips for managing your maintenance budget
Facilities managers know all too well that maintaining quality while controlling costs is a balancing act that requires...
Read More
31 Oct 2024 at 10:00 PM
A room-by-room guide to choosing the perfect hotel interior colours
Imagine walking into a hotel lobby that instantly makes you feel at ease — relaxed, but with an underlying energy that...
Read More
21 Oct 2024 at 10:00 PM
Avoid costly repairs with preventative maintenance plans for schools
It’s no secret that a well-kept physical environment fosters a safe, attractive and conducive learning space. A...
Read More
27 Jun 2024 at 11:00 PM
EWP services explained: your guide to effective use
In commercial painting, reaching high ceilings and other challenging areas has never been easier thanks to Elevated...
Read More
17 Jun 2024 at 11:30 PM
Your complete school maintenance checklist
School maintenance isn't just about keeping the lights on and the halls clean; it's about creating a safe and conducive...
Read More